Cement przyszłości. Jak budować w świecie zmiany klimatu?
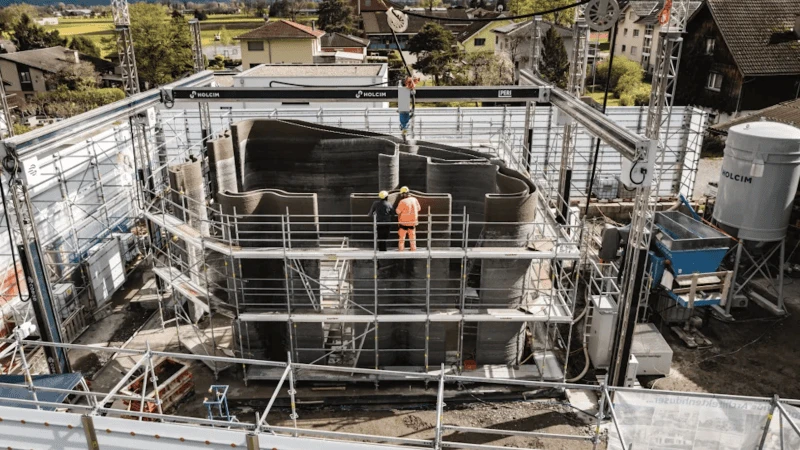
Według Międzynarodowej Agencji Energetycznej (IEA) przemysł cementowy nie wszedł nawet na drogę do realizacji scenariusza zerowej emisji netto do 2050 roku (NZE). W 2021 r. produkcja cementu odpowiadała za około 7 proc. rocznej antropogenicznej emisji dwutlenku węgla i prawie 0,6 tony CO2 na tonę cementu. Części emisji nie da się wyeliminować, dlatego branża poszukuje innych sposobów na tworzenie bardziej przyjaznych środowisku materiałów budowlanych i zmniejszenie śladu węglowego budynków.
Alicja Jankowska, Energetyka24: Dlaczego tradycyjna produkcja cementu jest tak wysokoemisyjna?
Clément Vert, Dział Różnicowania Cementu, Holcim Innovation Center w Lyon: Tradycyjny proces jest nadal bardzo powszechny – nie mówię tylko o Holcim, ale o każdym producencie cementu na świecie. Z kamieniołomu wydobywany jest wapień, czasem trochę gliny, ale głównie wapień. Następnie kruszy się go w młynie na drobny proszek, aby uzyskać mieszankę zwaną surową mączką surowcową. Taka mieszanka trafia następnie do pieca, który przekształca ją w klinkier.
Mączka surowcowa musi mieć odpowiednie proporcje czterech składników: krzemionki, glinu, tlenku żelaza i tlenku wapnia. Skład takiej mieszaniny można skorygować za pomocą alternatywnych surowców (ARM), aż do uzyskania prawidłowego składu. Po uzyskaniu właściwych proporcji surowiec wędruje do pieca, w którym płomienie podgrzewają go do temperatury około 1450°C. To właśnie tam, w kontrolowanych warunkach, zachodzi reakcja klinkieryzacji, która przekształca wapień w klinkier, główny reaktywny składnik cementu.
Po wyjęciu z pieca klinkier należy szybko schłodzić, aby zachować jego reaktywność (hartowanie utrzymuje amorficzną strukturę klinkieru, co zapewnia większą reaktywność niż uporządkowane struktury, które uzyskuje się po powolnym chłodzeniu – przyp. Energetyka24). Następnym krokiem jest zmieszanie go z pokruszonym siarczanem wapnia – najczęściej jest to gips. Następnie otrzymujemy CEM I – czysty cement portlandzki (ang. Ordinary Portland Cement, OPC). Wykazuje on bardzo dobrą wytrzymałość i jest to najbardziej powszechny sposób wytwarzania cementu. Można jednak wprowadzać zmiany na każdym etapie procesu, wykorzystując alternatywne materiały, takie jak beton z recyklingu lub odpady z innych gałęzi przemysłu – nawet z produkcji papieru – wykorzystując alternatywne źródła energii i paliwa alternatywne .
Dlaczego emisja gazów cieplarnianych z tego procesu jest tak wysoka? Który etap jest za to głównie odpowiedzialny?
Występują tutaj dwa źródła emisji CO2. Pierwszym z nich jest oczywiście zużycie energii podczas podgrzewania mączki surowcowej do bardzo wysokiej temperatury. Jeśli do tego celu wykorzystywane są paliwa kopalne, ta część odpowiada za około 30 proc. emisji. Większa część – około 60 proc. emisji – jest spowodowana chemiczną reakcją klinkieryzacji. W tym wysokotemperaturowym procesie z wapienia – czyli węglanu wapnia – usuwany jest dwutlenek węgla i otrzymywany jest tlenek wapnia. Tej części nie da się całkowicie wyeliminować.
Reakcja chemiczna: CaCO3 → CaO + CO2
Do jakiego stopnia można to zredukować?
Nad tym właśnie teraz intensywnie pracujemy. Już w tym momencie produkujemy i sprzedajemy na całym świecie cement o niskim śladzie węglowym – co najmniej 30 proc. CO2 mniej w porównaniu z tradycyjnym cementem produkowanym w tym samym zakładzie, ale może to być nawet mniej, w jednym z naszych francuskich zakładów osiągamy poziom redukcji o 50 proc.
Czytaj też
Redukcję emisyjności osiąga się poprzez zmianę źródła energii czy zmianę procesu?
W rzeczywistości chodzi o jedno i drugie, ponieważ nie ma jednego magicznego rozwiązania, które wyeliminowałoby wszystkie emisje. Potrzebujemy całego zestawu rozwiązań, które będziemy wykorzystywać na wszystkie możliwe sposoby. Mam teraz na myśli tylko redukcję na poziomie produkcji cementu, nie wliczając w to np. transportu do klienta.
Jako paliwo do procesu wykorzystujemy także odpady z innych procesów, np. z przemysłu rolniczego. Ważne jest, aby mieć odpowiednie rozwiązania dla każdej części świata, ponieważ lokalizacja ma ogromny wpływ na wybór możliwych i najbardziej wydajnych rozwiązań. Przykładowo we Francji mamy dostęp do drewna sosnowego i odpadów z rolnictwa. Natomiast w Nigerii, ze względu na panujące tam warunki klimatyczne, optymalne rozwiązania będą inne. Rosną tam inne rośliny, a lokalna gospodarka opiera się na innych działaniach.
Nawet jeśli zastąpimy wszystkie paliwa źródłami energii neutralnymi pod względem emisji dwutlenku węgla, nadal będziemy mieć emisje powstałe w wyniku reakcji. Rozwiązaniem jest stosowanie materiałów alternatywnych. Musi to być przede wszystkim materiał, który również będzie reaktywny, abyśmy mogli zbudować budynek w ten sam lub nawet bardziej wydajny sposób. Część z nich jest używana od dziesięcioleci, tak jak popioły lotne lub żużle stalowe, które są odpadami z innych procesów (odpowiednio produkcji energii elektrycznej zasilanej węglem i produkcji stali). Niektóre rozwiązania są bardziej innowacyjne, tak jak stosowanie gliny kalcynowanej, ale nie można całkowicie zastąpić klinkieru w cemencie. Innym sposobem jest z kolei wykorzystanie obiegu zamkniętego – materiały można odzyskiwać z rozbieranych budynków i recyklingować. W ten sposób uzyskuje się gruz betonowy, który po obróbce może być stosowany jako składnik cementu w postaci RCF (ang. recycled concrete fines).
Aby zmniejszyć nasz ślad węglowy, przeprowadzamy również renaturyzację terenów pogórniczych. Po zakończeniu wydobycia należy zregenerować ekosystem, przeprowadzić rekultywację gleby oraz nasadzenia. Taki teren można też wykorzystać do produkcji zielonej energii, instalując tam panele słoneczne lub wiatraki. Staramy się również poddawać recyklingowi całą wodę wykorzystywaną w procesie produkcyjnym.
Kolejną rzeczą jest wykorzystanie pojazdów elektrycznych do transportu surowców. Muszą one przewozić naprawdę ogromne ładunki, ale jednocześnie w naszej branży nie muszą być tak szybkie, więc są dla nas idealnym rozwiązaniem. Najlepiej jest oczywiście pozyskiwać surowce jak najbardziej lokalnie, by ograniczyć ślad węglowy z importu.
Obecnie intensywnie pracujemy nad optymalizacją transportu. Jeśli możemy obniżyć koszty transportu i wykorzystać na przykład łodzie, będziemy korzystać z łodzi, ponieważ jest to bardziej wydajne, jeśli chodzi o ślad węglowy w przeliczeniu na tonę cementu. Musi to być również uwzględnione w analizie cyklu życia (ang. Life Cycle Analysis, LCA), dzięki której można zaprezentować emisję CO2 i cyrkularność materiału w całym cyklu jego życia.
Jaki w Pana opinii najniższy poziom emisji z produkcji cementu można technicznie uzyskać?
Jeśli uda nam się połączyć naprawdę wydajne, neutralne pod względem emisji dwutlenku węgla paliwo oraz alternatywny sposób wytwarzania cementu poprzez obniżenie zawartości klinkieru, wierzę, że możemy osiągnąć naprawdę niską emisję CO2. Jednakże myśląc realistycznie, prawdopodobnie nadal pozostanie kilka procent emisji dwutlenku węgla, ponieważ i tak potrzebujemy klinkieru wytwarzanego tradycyjnie.
Zasadniczo są rzeczy, które możemy zrobić technicznie i są rzeczy, które możemy zrobić zgodnie ze standardem – to nie zawsze to samo. Duży wpływ mają przepisy obowiązujące w danym kraju. Ale przepisy się teraz zmieniają. Chce tego cała branża, chcą tego klienci. Widzimy tę zmianę w myśleniu, otrzymujemy pytania od konstruktorów, urbanistów, a także polityków. Ludzie z całego świata chcą obniżyć ślad węglowy budynków.
Czytaj też
Co można zrobić z tymi kilkoma procentami emisji dwutlenku węgla, by osiągnąć zerowe emisje netto w tym procesie?
Testujemy technologie wychwytywania, wykorzystania i składowania dwutlenku węgla (CCUS). Wychwycony CO2 można następnie wykorzystać do karbonizacji niektórych materiałów, aby poprawić ich właściwości, na przykład utwardzić je lub wydłużyć ich trwałość. Holcim współpracuje obecnie z wieloma start-upami, które pracują nad podobnymi rozwiązaniami. Jest to istotna część naszych strategii badawczo-rozwojowych. Ale dwutlenek węgla może być również wykorzystywany przez inne firmy do produkcji innowacyjnych paliw, działalności rolniczej, a nawet produkcji materiałów alternatywnych.
Wspominał Pan o recyklingu w branży budowlanej. W przypadku niektórych elementów budynków, np. konstrukcji stalowych, wydaje się to proste, a jak to wygląda w przypadku cementu?
Proces rozpoczyna się od oddzielenia elementów betonowych od reszty materiałów z budowli. Następnie wykonuje się inteligentne kruszenie, co oznacza, że możemy oddzielić składniki mineralne, kruszywa i skały. Dostosowując siłę kruszenia do twardości danego materiału, można wysortować poszczególne frakcje. Jeśli materiał jest twardy – jak skały – siła nacisku będzie za mała, by go skruszyć. Jeśli jest miękki – jak cement – zostanie zmielony. Następnie frakcja lekka – czyli proszek cementowy – jest oddzielana za pomocą przepływu powietrza, lekkie cząstki są porywane przez powietrze. Zmielony cement można dodać do świeżego, aby go rozcieńczyć, zachowując jego właściwości. Nawiasem mówiąc, ponownie wykorzystujemy również skały, zwykle po pewnych modyfikacjach.
Jest beton, z którego konstruowaliśmy budynki kiedyś i dzisiaj poddajemy go recyklingowi oraz beton, który zaczynamy produkować teraz, wiedząc z góry, że będzie poddany recyklingowi w przyszłości. Projektując nowoczesne budynki, branża budowlana powinna brać pod uwagę ich koniec życia i z założenia stosować materiały nadające się do recyklingu. Wkrótce analiza cyklu życia będzie standardem w Unii Europejskiej i trzeba w niej uwzględnić poziom cyrkularności. Wtedy okaże się, że nawet jeśli początkowe emisje z produkcji materiałów mogą być nieco wyższe, w całym cyklu życia można je obniżyć za pomocą recyklingu.
Dobrą wiadomością jest fakt, że w przeciwieństwie do tworzyw sztucznych z recyklingu odzyskiwany materiał budowlany ma tylko nieznacznie pogorszone właściwości. Budynki, które teraz rozbieramy, pochodzą z lat 50. lub 60. ubiegłego wieku, a wtedy technologie produkcji betonu były inne. Teraz projektujemy nowe materiały, od początku przeznaczone do recyklingu, więc ich właściwości będą jeszcze lepiej zachowane.
Czytaj też
Domyślam się, że istnieje również jakiś techniczny limit materiałów pochodzących z recyklingu, które można wykorzystać w budynku? Czy istnieje jakiś limit określony w przepisach?
Jestem inżynierem z działu R&D – dla mnie jedynym ograniczeniem powinno być to, co jest fizycznie możliwe. A faktem jest, że we Francji firma Holcim zbudował a kompleks mieszkaniowy wykonany w 100 proc. z betonu pochodzącego z recyklingu. To po prostu działa. W ten sposób udowodniliśmy, że takie konstrukcje są niezawodne. Tego rodzaju przykłady otwierają drzwi do zmiany przepisów, które obecnie – od czerwca 2023 r. – pozwalają na stosowanie do 35 proc. betonu z recyklingu. W 2030 r. mogłoby to być nawet 50 proc., a wkrótce nawet więcej. Całkowicie rozumiem, że powinny istnieć pewne regulacje, ponieważ warunki laboratoryjne i prawdziwe życie to nie to samo.
Tak naprawdę głównym wyzwaniem technicznym jest teraz logistyka. Infrastruktura potrzebna do kruszenia i rozdzielania materiałów zazwyczaj znajduje się w zakładzie, a nie na placu budowy, więc materiały trzeba transportować dwukrotnie – z rozbiórki i na teren nowej budowy. Najlepiej byłoby więc mieć takie instalacje w różnych miejscach w kraju. Być może w przyszłości będziemy mieć instalacje mobilne, które mogą pracować na miejscu, aby wykorzystywać materiały w tej samej lokalizacji.
Rozumiem też, że przy dzisiejszych technologiach istnieje możliwość wyprodukowania cementu o innych, nowych właściwościach.
Tak, zwłaszcza jeśli chodzi o wytrzymałość konstrukcji. To nad tym głównie pracują producenci od dziesięcioleci. Dzięki nowym materiałom możemy zmniejszyć zużycie betonu nawet o 50 proc. w niektórych przypadkach, przy zachowaniu tej samej wytrzymałości. A im mniej materiałów, tym mniejszy wpływ na środowisko.
Cały czas pracujemy też nad produktami o zupełnie nowych właściwościach. Możemy stworzyć beton, który starzeje się wolniej i będzie mniej wrażliwy na czynniki zewnętrzne. Stworzyliśmy już cement, który może być wykorzystywany w druku 3D i taki, który jest przepuszczalny dla wody, aby radzić sobie z powodziami w miastach i dostarczać wodę drzewom. Czasem lepiej jest zastosować beton wodoodporny – głównie w krajach, w których występuje pora monsunowa. Wdrożyliśmy takie rozwiązanie w Bangladeszu, aby chronić budynki przed ulewnymi deszczami.
Pracujemy również nad betonem, który jest przepuszczalny dla pola elektromagnetycznego, aby umożliwić np. bezprzewodowe ładowanie pojazdów elektrycznych w budynkach. Rozpoczęto już pilotażowe projekty testujące to rozwiązanie. W ten sposób tworzymy synergię między różnymi branżami i możemy jeszcze lepiej przysłużyć się środowisku.
Czytaj też
Czy do produkcji cementu wykorzystywane są już również materiały pochodzenia roślinnego?
W Holcim chcemy gromadzić ludzi, którzy myślą nieszablonowo, więc niektóre start-upy, z którymi współpracujemy, pracują z biomasą. Jeden z nich tworzy cement wzbogacony o wióry drzewne, czyli odpady z procesu produkcji drewna. Dzięki temu staje się on neutralny pod względem emisji dwutlenku węgla. Ogólnie rzecz biorąc, prowadzone są szeroko zakrojone badania w tym zakresie. Materiały pochodzenia roślinnego mogą przynieść zupełnie nowe właściwości.
To brzmi, jakby produkcja cementu mogłaby współpracować z paludikulturą, czyli sposobem produktywnego użytkowania gruntów na mokrych i nawodnionych torfowiskach, które musimy przecież chronić. Jedną z głównych roślin są tam turzyce, które są bardzo bogate w krzemionkę – jeden z pierwiastków potrzebnych do produkcji cementu
Dokładnie, to jedna z roślin, które badamy. Ogólnie rzecz biorąc, badamy głównie odpady (z rolnictwa, procesów uzdatniania wody itp.). Największy problem z roślinami jest taki, że ich skład zmienia się w czasie – ta sama trawa, od tego samego dostawcy, skoszona wiosną i jesienią będzie inna. Zależy to od warunków, w jakich roślina rosła, pogody, dostępu do wody, obecności owadów itp. Do rozwiązania problemu „niestabilności” takich surowców, wykorzystujemy m.in. sztuczną inteligencję i uczenie maszynowe, aby móc szybciej dostosowywać się do wahań w składzie i działać z szeroką gamą półproduktów.
Na koniec mała ciekawostka naukowa – niezwykle fascynującą rośliną jest też proso rózgowate (Panicum virgatum). Znajduje się w centrum wszystkich badań nad wykorzystaniem biomasy do produkcji cementu, wszyscy nad tym pracują. Rośnie bardzo szybko i wymaga jedynie niewielkich ilości wody. Jest również kompatybilna z klimatem wielu kontynentów, a efektywność energetyczna jej spalania jest naprawdę wysoka. To może być przyszłość cementu domieszkowanego materiałami pochodzenia roślinnego.