Fundament świata musi odejść. Trwa batalia o bezemisyjny beton [ANALIZA]
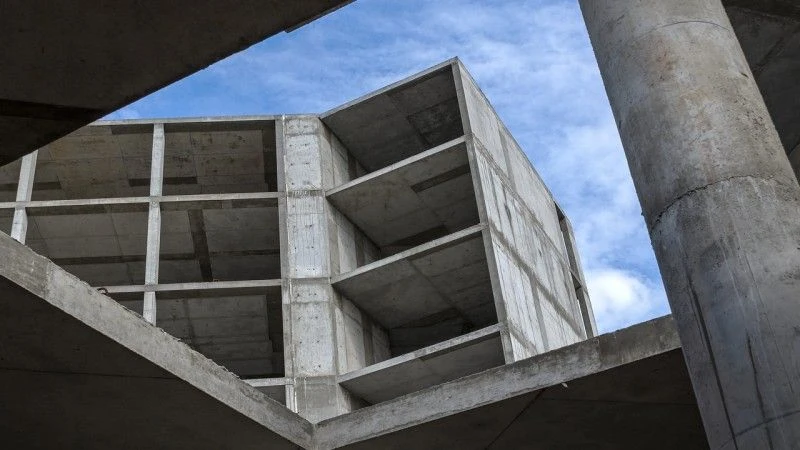
Produkcja betonu, z którego zbudowany jest nasz świat, odpowiada za aż 7% globalnych emisji CO2. Pojawiło się światełko w tunelu – dwukrotnie mniej emitujący LC3, czyli wapienny cement gliniasty.
Rioclaro, Kolumbia. To tutaj znajduje się największa fabryka cementu w kraju. Argos, bo tak się nazywa, może produkować nawet 2,3 miliona ton cementu rocznie, używanego do budowy wszystkiego, od stadionów i tam po drapacze chmur i mosty. To pomogło uczynić Argos największym producentem cementu w Kolumbii - ale także głównym producentem emisji dwutlenku węgla.
Cement i CO2 wylewa się z Rioclaro nieprzerwanie od ponad 20 lat, kiedy prezes Argos spotkał naukowca o nazwisku Karen Scrivener, która miała prosty pomysł: zmienić recepturę cementu na glinę i zmniejszyć ślad węglowy. Nazwała go LC3, czyli wapiennym cementem gliniastym.
Po czterech latach remontu, odnowiony zakład w Rioclaro został w tym roku uruchomiony, wykorzystując glinę wydobywaną około 10 mil dalej i przetwarzaną w nowo wybudowanym piecu. Argos twierdzi, że technologia obniża zużycie energii o 30% i zmniejsza emisję dwutlenku węgla o prawie połowę. "Mniej CO2 oznacza mniej węgla lub paliwa, więc jest to bardziej opłacalne. Zmiany środowiskowe zachodzą najlepiej, gdy istnieje również zachęta ekonomiczna" – mówi Tomás Restrepo, szef działu firmy w Kolumbii.
Trudno przecenić znaczenie uporządkowania przemysłu cementowego. Ludzie zużywają tyle samo cementu co żywności - 4 miliardy ton rocznie - a jego produkcja odpowiada za około 7% globalnej emisji dwutlenku węgla.
Redukcja będzie wymagała niezliczonych małych kroków, od zmniejszenia emisji dwutlenku węgla przez cementownie po zmianę przepisów, tak aby bardziej realistycznie uwzględniały one potrzeby konstrukcyjne budynków.
Beton "jest bardzo tani, a ludzie systematycznie go nadużywają" - mówi Bloombergowi 62-letnia Scrivener, profesor na Ecole Polytechnique Fédérale w Lozannie w Szwajcarii. "Możemy zredukować produkcję cementu, a następnie ilość cementu umieszczanego w betonie i ilość betonu włożonego do budynku" - dodaje.
Jasne, istnieją alternatywy: Norwegia zbudowała 280-metrową wieżę z drewna, a naukowcy eksperymentują z bambusem, przetworzonymi odpadami budowlanymi, a nawet grzybami, aby opracować bardziej ekologiczne materiały budowlane. Jednak wizja całkowitego zastąpienia betonu w najbliższym czasie jest nierealistyczna, zwłaszcza tam, gdzie nastąpi największy rozwój w nadchodzących dziesięcioleciach - w Chinach, Indiach czy Nigerii - które mają niewiele możliwości wyboru innych niż beton w swoich domach, szpitalach i autostradach.
Warto dodać, że Chiny w latach 2011-2013 zużyły więcej cementu niż USA w całym XX wieku. Widzimy zatem skalę wyzwania przed którym staje branża budowlana.
Podwójne emisje
Cement powstaje poprzez zmieszanie sproszkowanego wapienia z kilkoma innymi składnikami i spalenie go w temperaturze 1450 stopni Celsjusza. Rezultatem jest kamienista substancja zwana klinkierem, która przypomina brykiety z węgla drzewnego używane w przydomowych grillach. Klinkier jest mielony na proszek i łączony z kilkoma innymi minerałami w celu uzyskania cementu.
Ten proces niewiele się zmienił od czasu, gdy angielski murarz Joseph Aspdin w 1842 roku opatentował to, co nazwał cementem portlandzkim. , Emituje CO2 podwójnie. Zarówno paliwo używane do spalania w piecach, jak i sam wapień - utworzony miliony lat temu z koralowców morskich i skorupiaków - podczas spalania uwalniają dwutlenek węgla. Na każdą tonę wyprodukowanego cementu do atmosfery dociera 600-800 kg dwutlenku węgla.
Beton z kolei powstaje poprzez połączenie cementu z piaskiem, kamieniami, i wodą. Aspdin, brytyjski murarz, wybrał nazwę cement portlandzki, ponieważ czuł, że jego gotowy produkt przypomina kamień portlandzki, poszukiwany materiał budowlany w ówczesnej Anglii.
Jego mikstura pozwoliła budowniczym zrezygnować z ciągnięcia ogromnych kawałków skały. Zamiast tego beton jest łatwo transportowany jako lepki płyn, który można wylewać i formować w chodniki, autostrady, mosty, fundamenty budynków, ściany, sufity i prawie wszystko, czego dusza zapragnie. Przynajmniej odrobina betonu trafia do praktycznie każdej konstrukcji w uprzemysłowionym świecie.
Przełom?
LC3 może zmniejszyć ślad węglowy przemysłu na dwa sposoby: glina zawiera bardzo mało węgla, więc prawie nic nie jest uwalniane podczas podgrzewania i można ją spalać w łatwiejszej do opanowania temperaturze 800 C, zużywając mniej paliwa. "Koniec końców mniej wapienia spalanego jest przy LC3, a to właśnie wapień generuje większość emisji CO2" - mówi Scrivener. "Jasne, do tego potrzebne jest ciepło, ale nie tak dużo, jak w przypadku cementu portlandzkiego" – dodaje.
Regulacje
Według niej wprowadzenie podatków od emisji dwutlenku węgla i schematów handlowych będzie stymulować adopcję. W UE zakłady przemysłowe, takie jak huty i cementownie, mogą wydzielać pewną ilość dwutlenku węgla. Jeśli emitują mniej, mogą sprzedać swoją dodatkową moc, ale jeśli przekroczą swoją kwotę, muszą kupić dodatkowe zezwolenia na emisję CO2.
W ciągu ostatnich trzech lat ceny emisji dwutlenku węgla w Europie wzrosły ponad trzykrotnie i prawdopodobnie będą nadal rosły, gdy UE będzie obniżać limity. Mocne tąpnięcie nastąpiło na początku epidemii koronawirusa (spadek poniżej 20 euro za tonę), ale we wrześniu ceny powróciły na poziom sprzed pandemii.
Na całym świecie istnieją praktycznie nieograniczone zasoby gliny, z której wiele jest już wydobytych i dostępnych jako materiał odrzucony przez przemysł ceramiczny lub producentów papieru, którzy używają jej do powlekania. Wielu wytwórców betonu oprócz żwiru i piasku ma w swoich kamieniołomach tony gliny.
Fabryka w Argos jest pierwszym zakładem produkcji gliny kalcynowanej na dużą skalę, ale na całym świecie budują się kolejne. Największy producent cementu w Europie, LafargeHolcim, spodziewa się w przyszłym roku dodać piece gliniane w fabrykach we Francji i Szwajcarii. Cimpro, producent portugalski, przeprowadza testy w zakładzie LC3 w Wybrzeżu Kości Słoniowej.
Inne drogi
Nie wszyscy są tak entuzjastyczni. Beton wykonany z LC3 często wykazuje mniejszą wytrzymałość niż tradycyjne receptury w ciągu pierwszych siedmiu dni, mówi Vanderley John, profesor materiałów budowlanych na Uniwersytecie w São Paulo w Brazylii. Wytrzymałość można nadrobić później - pełne związanie betonu zajmuje miesiąc lub dłużej - i można ją wzmocnić dodatkami lub gliną wyższej jakości. Ale opóźnienia są kosztowne. "Im krótszy okres budowy, tym lepszy zwrot dla inwestorów" - mówi John.
Z roku na rok powstają kolejne alternatywy. LC3 ma dość ostrą konkurencję. LafargeHolcim we współpracy z amerykańskim start-upem Solidia Technologies opracował nowatorską formę betonu, która zmniejsza całkowity ślad węglowy nawet o 70%. Proces polega na wykorzystaniu innego składu surowców do produkcji cementu w niższych temperaturach i dodaniu CO2 zamiast wody w celu uformowania betonu.
Heidelberg Cement odkrył alternatywną technologię klinkieru o nazwie TermoCem. Ma ona zmieniony skład chemiczny i niższe temperatury spalania. Firma podaje, że emisja CO2 jest o 30% niższa w porównaniu z konwencjonalnym klinkierem, a zużycie energii można zmniejszyć o około 15%.
Tarmac, spółka zależna CRH Plc, jest uczestnikiem LEILAC, projektu Low Emission Intensity Lime and Cement. Projekt koncentruje się na opracowaniu kalcynatora, który może bezpośrednio oddzielać i wychwytywać około 95% CO2 uwalnianego z wapienia podczas przekształcania go w klinkier. Jest to część projektu UE Horyzont 2020.
Zespół badawczo-rozwojowy firmy CEMEX w Egipcie wprowadził na rynek nowatorski produkt cementowy, który może zmniejszyć emisję dwutlenku węgla o 15–20%. Produkt wykorzystuje klinkier zawierający około 20% naturalnego materiału pucolanowego (popiół wulkaniczny) po obróbce mechanicznej i chemicznej. Ponadto firma jest zaangażowana w kilka europejskich projektów badawczych, których celem jest wychwytywanie, składowanie i utylizacja dwutlenku węgla. Należą do nich Solpart, który zamierza pilotować wysokotemperaturowy proces solarny odpowiedni do kalcynacji surowców cementowych oraz DESTINY, którego celem jest wykorzystanie energii mikrofalowej w kalcynacji gliny do stosowania w cementach o niskiej zawartości klinkieru.
1,5 tys. patentów
Jednym z miejsc, gdzie takie pomysły powstają jest położone na obrzeżach francuskiego Lyonu laboratorium badawcze LafargeHolcim. Około 200 naukowców codziennie głowi się nad tym, jak do 2030 roku obniżyć emisje giganta budownictwa o 15%.
"Ponad 40% z 1500 patentów Lafarge na cement ogranicza emisję dwutlenku węgla, musimy promować bardziej ekologiczne rozwiązania" - mówi Bloombergowi szef badań Edelio Bermejo. "Ale musimy to zrobić bez utraty jakości" - dodał.
Dziesiątki projektów laboratorium obejmują druk 3D elementów betonowych. Niedawno ogłoszono, że LafargeHolcim wraz z GE Renewable Energy i Cobod będą drukować super-wysokie turbiny do wiatraków, które mają sięgać nawet 200 metrów. Ma to pomóc w „dosięganiu” silniejszych wiatrów.
Wśród projektów są również koncepcje tj. alternatywne sposoby ogrzewania pieców cementowych, takie jak spalanie śmieci lub starych opon. Jedna grupa tworzy beton, który wymaga mniej wody. Inny dodaje do mieszanki wióry drzewne. Trzeci to poszukiwanie lepszych sposobów mielenia piasku i żwiru, tak aby do wykonania betonu potrzeba było mniej cementu.
Zastąpienie betonu to zadanie arcytrudne. Mimo, że koncepcji jest zatem bez liku, przypomina ono tworzenie ludzkiej piramidy, gdzie wszystkie elementy, od jakości materiału, przez jego emisyjność, aż po cenę wytworzenia, muszą osiągnąć balans i harmonię, i to taką, która będzie konkurencyjna względem starego dobrego betonu, na którym stoi nowoczesny świat.